Explosion protection: zones, guidelines and solutions
Gases, dust or heat sources in the laboratory can lead to a considerable risk of explosion time and again. To minimise these risks and ensure the safety of everyone involved, effective explosion protection (ex-proof) is essential.
We will be happy to help you with our in-depth expertise and innovative equipment. Continue reading to find out about explosive zones, the relevant guidelines, and which solutions Waldner can offer to ensure your laboratory and systems have the best explosion protection.
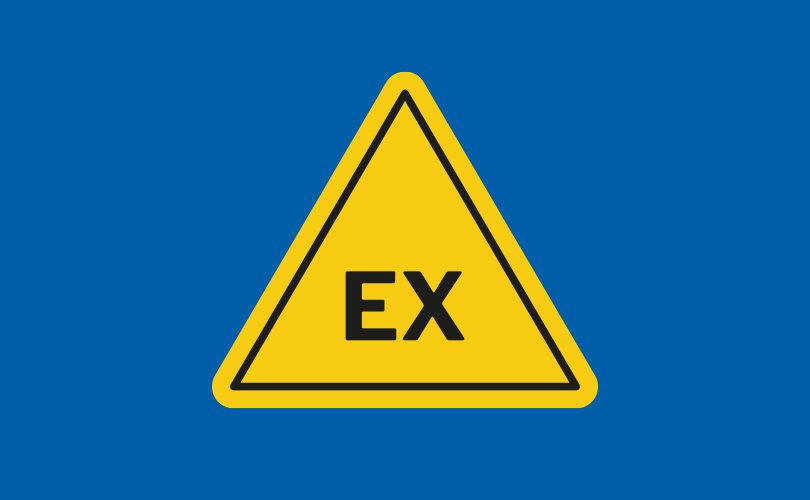
Why is explosion protection needed?
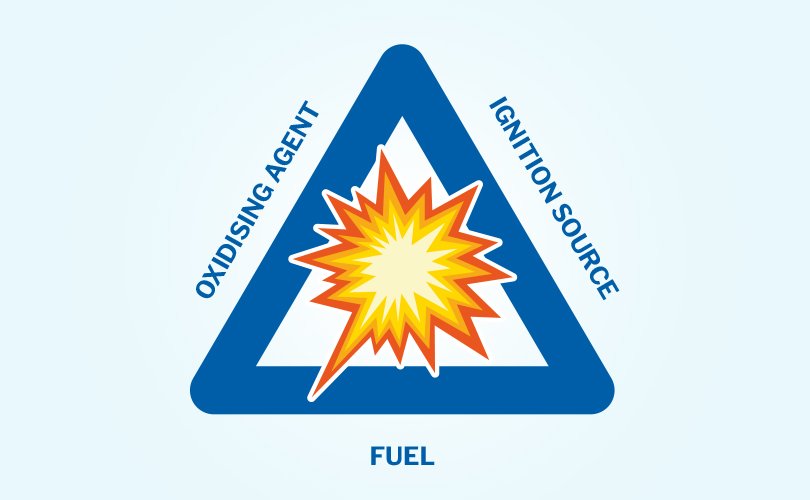
For an explosion to occur at all, three components are needed – what is known as the ignition triangle:
- Combustible material: specific gases, vapours, dust, or fibres
- Oxidising agent: primarily oxygen, but also chlorine for example
- Ignition source: e.g., a spark, a hot surface, or electrostatic charge
If the combustible material mixes with the oxidising agent at a certain concentration, an explosive mix occurs. If an effective ignition source is then added, this can explode.
Use waldner for your explosion protection
Safety concerns always take priority when we develop our laboratory technology. Thanks to our innovative, technological solutions, you can reliably meet the strict requirements of the ATEX directive. Our in-house Explosion Protection department will be happy to advise you on planning and fitting explosion protection in your facilities.
Waldner laboratory fume hoods are fully capable of conducting electrostatic energy, thus completely eliminating the most common ignition source, namely electrostatic charges. Our laboratory fume hoods also have an innovative touch panel, which is easy to operate and displays all the critical information such as room temperature and the air flow rate of the extracted air at a glance.
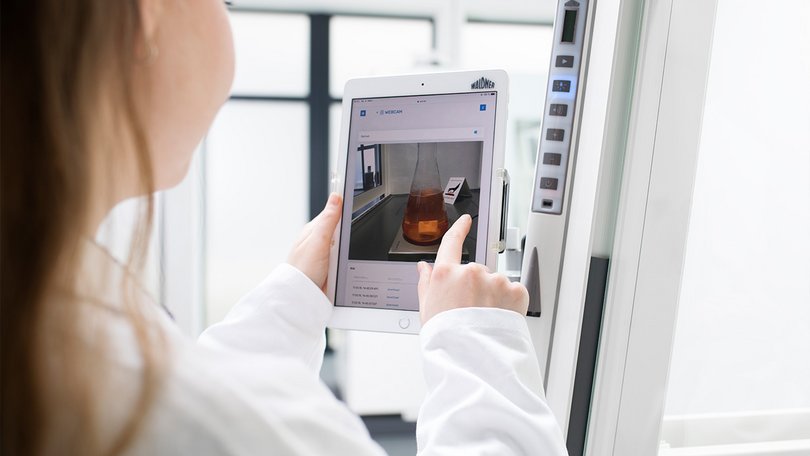
We will develop a tailored concept for your new laboratory that covers all explosion protection requirements. Our years of experience have enabled us to perfectly combine safety requirements, functionality and sustainability. If required, we will also be happy to assist you beyond the planning phase with laboratory construction.
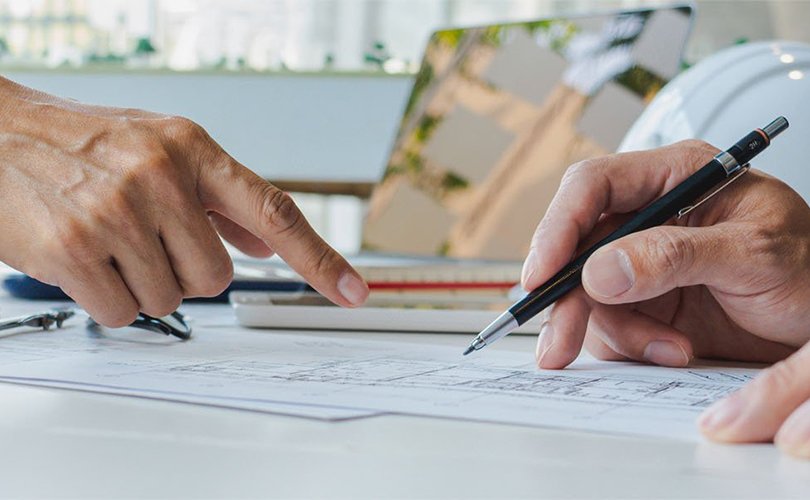
In collaboration with the German Technical Inspection Authority TÜV Süd, Waldner has devised a sophisticated Quality Management system. All those involved in the process are specially trained “professional electricians with specialist knowledge of explosion protection”, who attend annual training courses to ensure their expertise remains up-to-date. The Waldner team also promises excellent customer service incorporating the assembly, maintenance and servicing of all ex-proof laboratory facilities throughout the entire lifecycle.
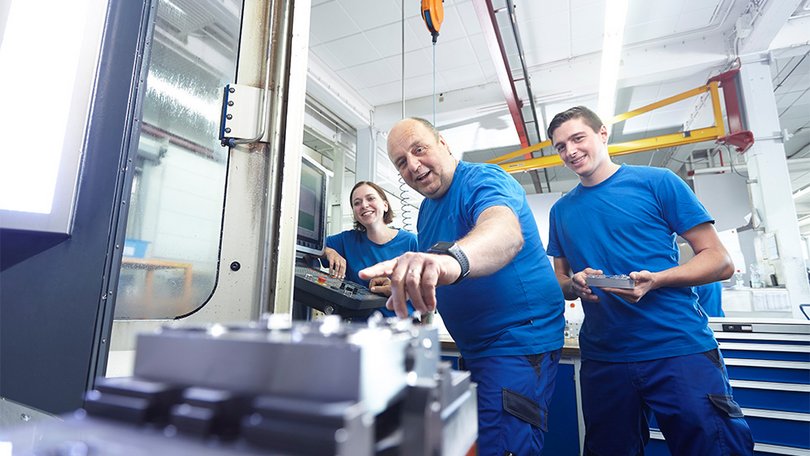
Want to know more?
Let’s find out how to create a unique, optimal solution for your needs.
Risk analysis as a prerequisite
The aforementioned mix of combustible material, oxidising agents and ignition source(s) frequently occur in industry, laboratories and similar areas, which means reliable explosion protection is essential. To identify these risks, a risk analysis needs to be conducted. In Europe, all plant operators are required to do this. The analysis identifies potential hazards, and forms the basis for any measures required to prevent a risk of explosion.
Depending on the complexity of the plant, the type of combustible materials, the size of the company, existing expertise in the company, and the local legal requirements, these analyses are performed by internal or external experts. Targeted explosion protection measures are then defined.
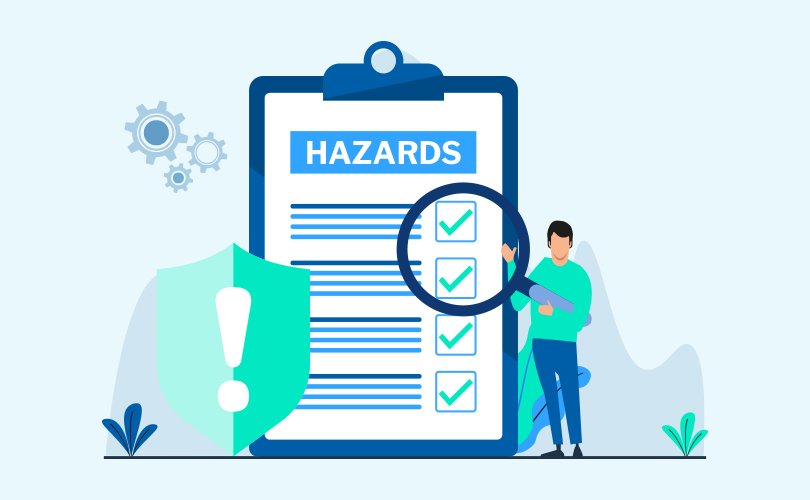
What ex zones are there?
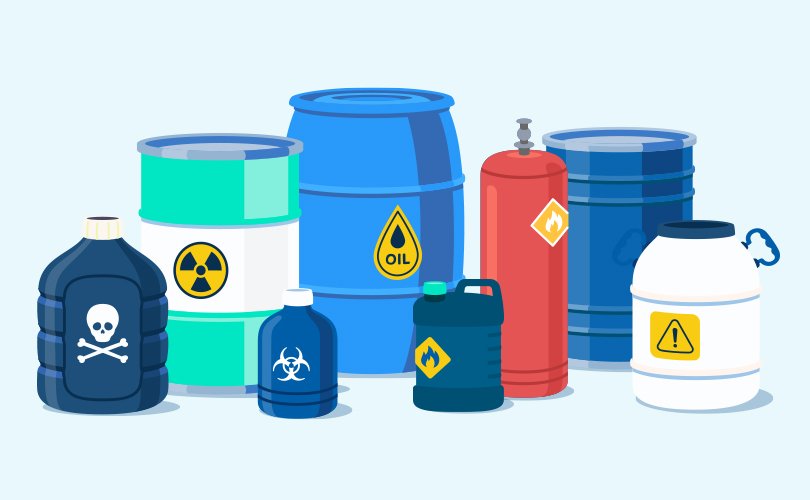
The risk of explosion is not the same in every area around the risk source. For this reason, the hazard areas are categorised as ex zones (areas at risk of explosion). These define how high the explosion risk is in the respective zone. The risk analysis forms the basis for how the zones are categorised.
The ex zone categorisation depends on the type of potentially explosive materials located there. This might be a mix of air and combustible gases, vapours or mists or a mix of air and combustible dust. The resulting explosive atmosphere is split into three zones.
EX zones for gases, vapours and mists
Where the atmosphere consists of air and gases, vapours or mists, a distinction is made between ex zones 0, 1 and 2.
- Zone 0: An explosive atmosphere is present continuously or for long periods or frequently.
- Zone 1: During normal operation, an explosive atmosphere may occasionally form.
- Zone 2: An explosive atmosphere does not normally occur or only occurs for a short period.
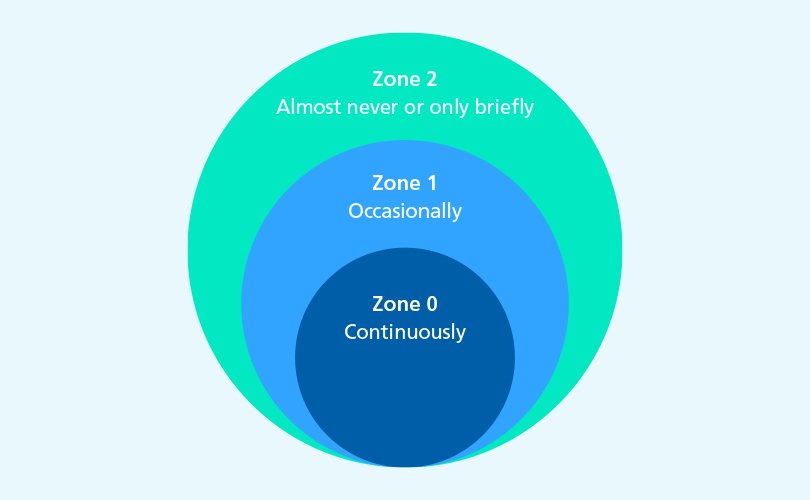
Ex zones for dust
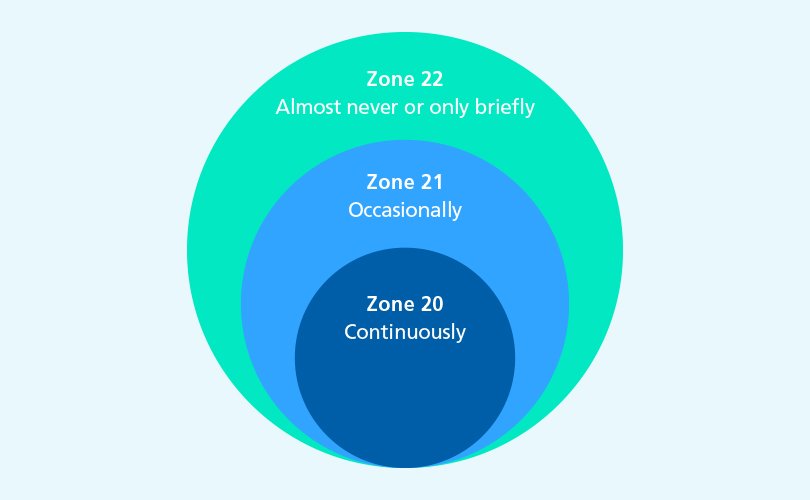
Where the atmosphere consists of air and dust, a distinction is made between ex zones 20, 21 and 22.
- Zone 20: This is an area in which an explosive atmosphere is present continuously or for long periods or frequently.
- Zone 21: An explosive atmosphere may occasionally form during normal operation.
- Zone 22: An explosive atmosphere does not normally occur or only occurs for a short period during normal operation.
In Europe, the ex zones are derived from the ATEX directive. For this reason, they are also referred to as ATEX zones.
Explosion protection: directives and guidelines (atex)
In the EU, the most important directive concerning explosion protection is the ATEX Directive (ATmosphères EXplosives). This incorporates two different areas: the ATEX Product Directive 2014/34/EU and the ATEX Operating Directive 1999/92/EC.
The ATEX Product Directive 2014/34/EU defines the requirements for the circulation of equipment, components and protection systems for use in potentially explosive areas. This includes both electrical and non-electrical products that could trigger an explosion as a result of the build-up of heat or electrostatic charge.
This explosion protection directive is intended for manufacturers, who are obliged to meet and demonstrate certain safety and health requirements. As of 30 June 2003, only products that meet these requirements may still be sold. The primary aim of this directive is to protect persons working in potentially explosive environments.
In addition to the ATEX Product Directive, there is also the ATEX Operating Directive (officially: Directive 1999/92/EC). This governs the operation of equipment, components and protection systems for use in potentially explosive areas. The directive intends to minimise the risk of an explosion while at the same time improving the health protection and safety of employees.
To achieve this, there are several measures that employers are required to put in place. These include the following:
- Avoid an explosive atmosphere
- Avoid effective ignition sources
- Limit the impact of possible explosions
The next section of this guide outlines how this can be implemented in detail.
Outside Europe, explosion protection is governed by the IECEx System. This is the important explosion protection guideline on the international stage. It focuses on the evaluation and certification of equipment and services in potentially explosive atmospheres.
Explosion protection measures
There is an increased risk of explosion in the defined ex-proof areas, which is why the ATEX Operating Directive mentioned earlier is used. This comprises three pillars:
- Primary explosion protection: The formation of an explosive atmosphere should be avoided.
- Secondary explosion protection: The ignition of an explosion should be prevented.
- Tertiary explosion protection: This is about minimising the damage caused if an explosion actually occurs.
Read on to find out which measures are covered under primary, secondary and tertiary explosion protection.
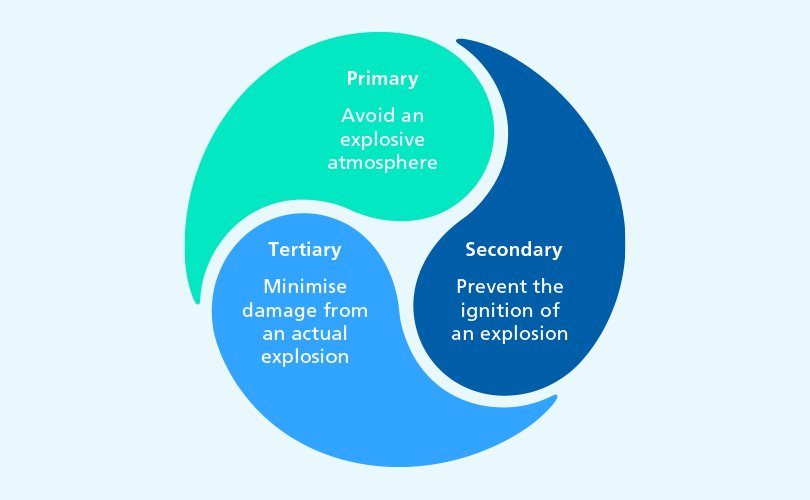
Primary explosion protection
This category controls the conditions that can lead to the formation of an explosive atmosphere, therefore preventing a possible explosion. This can be achieved in various ways:
Secondary explosion protection
Secondary explosion protection aims to prevent an explosive atmosphere being ignited. This means eliminating possible ignition sources (e.g., sparks, flames, electromagnetic fields, electrostatic discharge) . This is used in addition to primary explosion protection, as an explosive atmosphere can often not be completely avoided. Secondary explosion protection measures include:
Tertiary explosion protection
If an explosion has already occurred, tertiary explosion protection applies. This covers measures and strategies to minimise the impacts of an explosion on people, the facility and the environment and to manage the consequences of an explosion. Measures may include:
Products for the ex zone
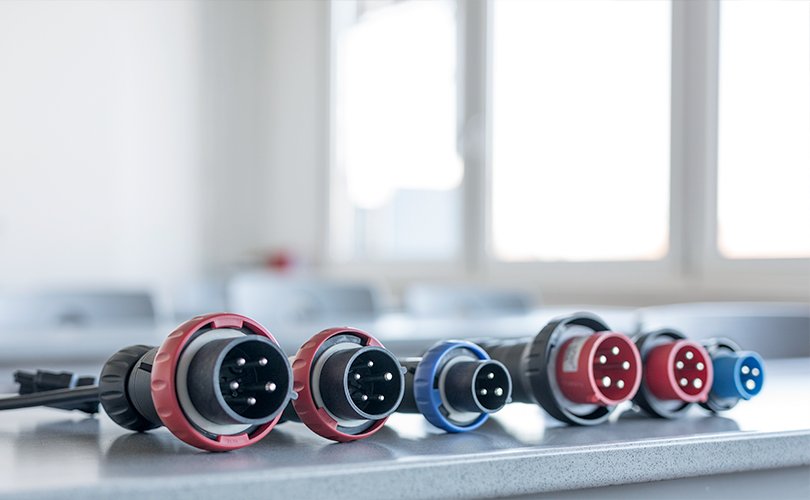
If you’re intending to purchase products – whether equipment or other components – for a work environment with an explosive atmosphere, it’s important to note the certification mark. Not every product is equally suitable for all ex zones: It’s therefore essential that the product in question is approved for the respective ex zone.
There are also products that are not certified. These are either completely unsuitable for the ex-proof area or do not have to be certified because they are not covered by the ATEX directives. If you’re unsure whether a product is right for your application, you should always ask the manufacturer to confirm its suitability.
Explosion protection documents
Companies that have an increased risk of explosions are required to compile an explosion protection document. This generally includes the following:
- Detailed assessment of potential hazards
- In-house ex zone classification
- Specific risk mitigation measures
- Training plans
- Emergency plans
- Maintenance and inspection guidelines
- Responsibilities
- Updates to the explosion protection document
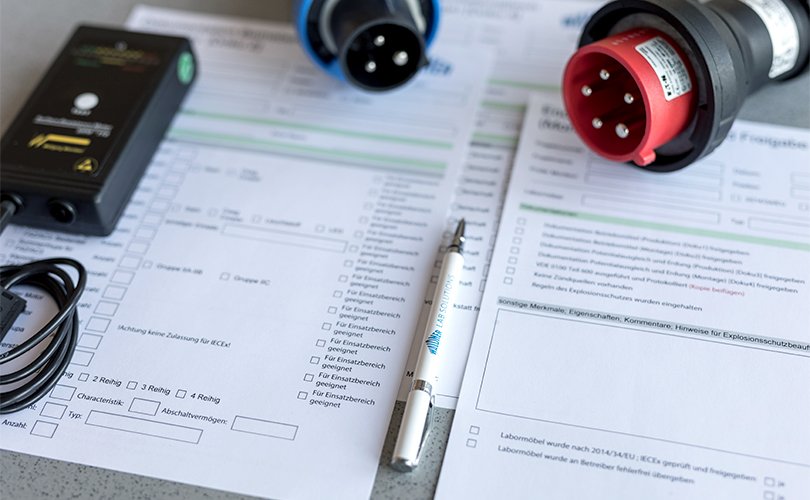
Explosion protection is a fundamental prerequisite
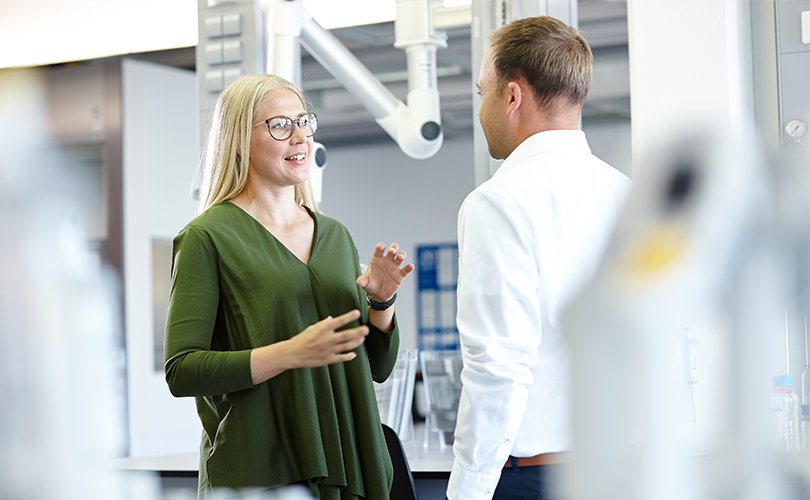
Explosions can occur wherever the work involves combustible substances, whether gases, vapour, dust, or fibres. Effective explosion protection is therefore indispensable in laboratories and plants of any type to ensure the safety of employees and adhere to the applicable ATEX directives.
Primary, secondary and tertiary explosion protection is crucial. As such, explosive atmospheres must be prevented, possible ignition sources eliminated, and any damage minimised if an explosion occurs despite all precautions. We will be happy to help you implement any explosion protection measures in your laboratory. Just get in touch.
FAQ
The term explosion protection or ex-proof refers to protection against the risk of explosion caused by an explosive atmosphere. This exists if a combustible material mixes with an oxidising agent in sufficient quantity, and the reaction is triggered by an ignition source.
Ex-proof areas or ex zones are areas where an explosive atmosphere occurs at least temporarily. Ex-proof areas are areas that are protected against a potential explosion. There is no risk of explosion here.
In the EU, two laws are important: the ATEX Product Directive 2014/34/EU and the ATEX Operating Directive 1999/92/EC. These govern all the important framework conditions for preventing and handling explosions. On the international stage, explosion protection is governed by the IECEx system.
There are various explosion protection measures: prevention, limiting the effects of potential explosions, and managing the consequences of an explosion. All companies in which an explosive atmosphere can occur are required to implement these measures.
The explosion protection document
- identifies specific risks in the company that are associated with the handling, storage, and processing of combustible substances such as gases, vapour, dust, or fibres.
- defines precautions that minimise the risk of explosions and ensure the safety of employees, facilities and the environment.
- sets out measures and strategies to minimise the impact of an explosion on people, the facility and the environment after an explosion occurs and to manage the consequences.
This document is mandatory for all companies in which explosions can occur.
You might also be interested in