GMP-compliant operation for pharmaceutical production areas
GMP-compliant operation requires reliable airborne germ monitoring. A permanently installed airborne germ monitoring system offers major advantages over mobile air samplers in class A and B clean rooms.
High reproducibility, minimal interruptions to the production process with a high degree of operational reliability, simple integration into the machine’s own HMI including integration into a parent process control system, standard quality-relevant analyses: asip compact combines all the requirements for GMP-compliant airborne germ procedures in a pharmaceutical production facility in the smallest possible space.
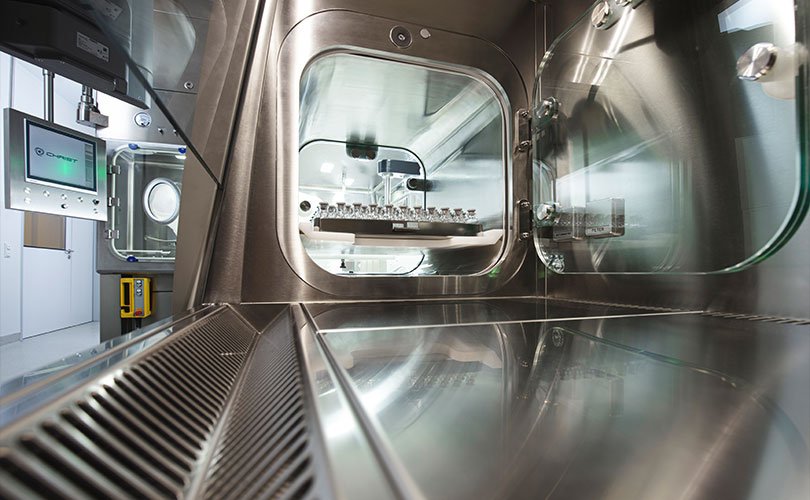
Benefits of asip – the integrated measurement system
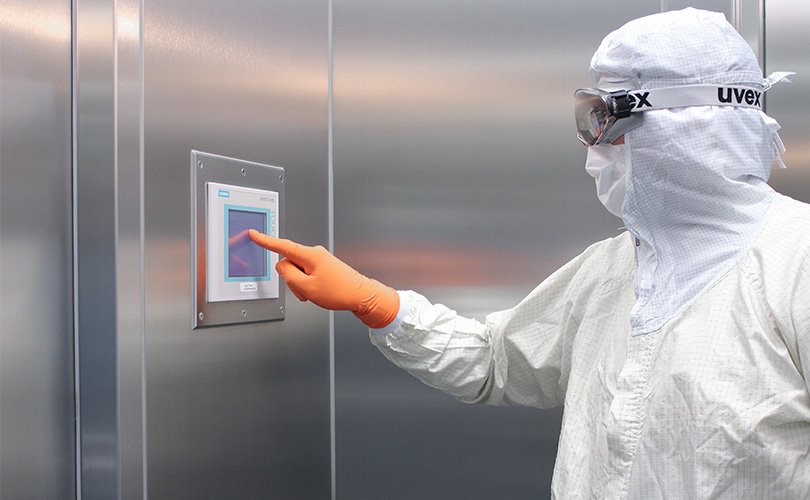
- Prevent contamination
The risk of contamination is eliminated by avoiding the introduction of devices in the clean room. Cross-contamination by used measuring equipment is also effectively prevented. - High reproducibility of measuring points
Thanks to permanently installed piping, the measuring point is always clearly defined, so the operator doesn’t have to search for a plan. This ensures high reproducibility and precision.
Minimal interruptions to production process
You may also be interested in